The Best CNC for Cutting Aluminum: A Comprehensive Guide
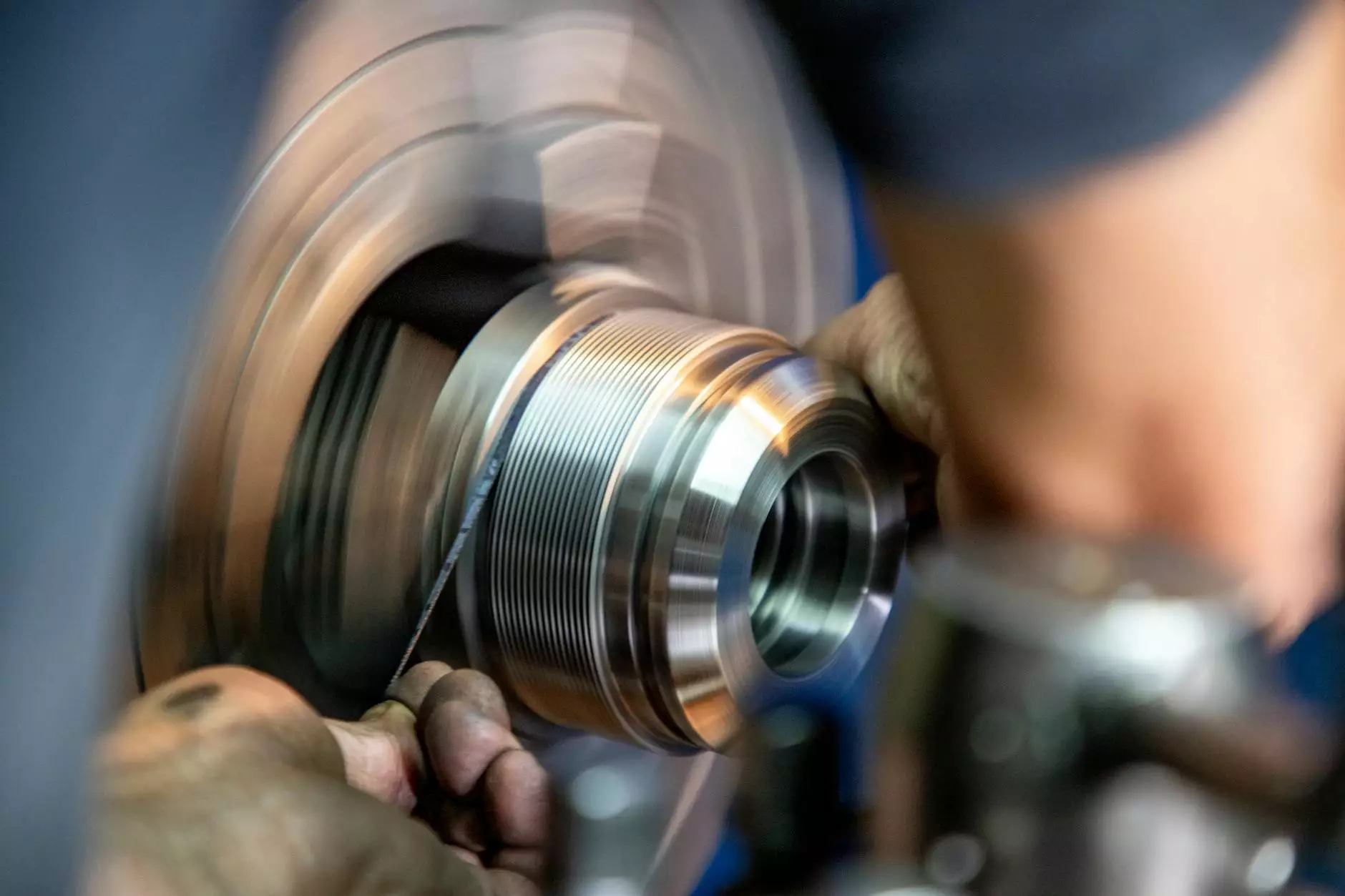
Introduction
When it comes to precision machining, CNC machines have revolutionized the manufacturing process. Among various materials, aluminum is widely used in industries due to its lightweight and strength. For businesses seeking the best CNC for cutting aluminum, understanding the specific requirements to achieve high-quality results is crucial. In this article, we will delve into the best CNC machines available on the market, their features, and how to select the ideal one for your business needs.
Why Choose CNC Machining for Aluminum?
Aluminum is a versatile metal used in industries ranging from aerospace to automotive, and its demand continues to grow. Understanding why CNC machining is favored for aluminum is essential:
- Precision: CNC machines ensure precise cuts, which is critical for applications requiring tight tolerances.
- Efficiency: Automated processes lead to faster production times compared to manual machining.
- Versatility: CNC machines can handle complex shapes and designs with ease, making them perfect for custom parts.
- Material Waste Reduction: The accuracy of CNC machining reduces material waste, lowering production costs.
Top Features of the Best CNC for Cutting Aluminum
When evaluating CNC machines for aluminum cutting, several features should be taken into consideration:
1. Cutting Speed
The cutting speed of a CNC machine plays a vital role in its ability to handle aluminum effectively. Look for machines that offer high RPM rates to facilitate faster cutting without compromising quality.
2. Spindle Power
A powerful spindle is necessary for maintaining torque during aluminum cutting. Opt for a machine with a robust spindle motor to handle various aluminum types and thicknesses.
3. Tooling Options
The availability of suitable tooling can greatly enhance the cutting process. Ensure that the CNC machine supports different types of tools specifically designed for aluminum to maximize efficiency.
4. Build Quality and Rigidity
The overall build quality impacts the precision and durability of a CNC machine. A rigid frame minimizes vibrations and enhances accuracy, which is essential for intricate aluminum work.
5. Software Compatibility
Modern CNC machines operate using sophisticated software. Check for compatibility with popular CAD/CAM software to ensure smooth operation and design integration.
Recommendations for the Best CNC Machines for Cutting Aluminum
Based on extensive research and industry feedback, here are some of the best CNC machines suitable for cutting aluminum:
1. Tormach PCNC 440
The Tormach PCNC 440 is an excellent choice for small shops and prototyping. Its user-friendly interface and powerful capabilities make it ideal for cutting aluminum with precision and ease. Key features include:
- Compact design with a small footprint.
- Variable-speed spindle for versatile machining options.
- Affordable pricing for small business budgets.
2. Haas Mini Mill
The Haas Mini Mill is a popular model known for its reliability and performance. This CNC machine can handle a range of materials, but it excels at cutting aluminum thanks to its high-speed capabilities. Notable features include:
- High-speed spindle for rapid cutting.
- Large work envelope to accommodate bigger projects.
- Haas' intuitive control systems for easy operation.
3. ShopSabre CNC Routers
ShopSabre CNC Routers are highly regarded for their precision and speed, making them a solid choice for aluminum cutting. This machine is ideal for businesses looking for scale and flexibility. Key characteristics are:
- High-resolution stepper or servo motors for enhanced accuracy.
- Fast feed rates for increased productivity.
- Robust build that withstands heavy use.
4. CNC Masters CNC Mill
The CNC Masters CNC Mill combines affordability with precision, enabling shops to carry out custom aluminum jobs easily. Its features include:
- Durable construction tailored for longevity.
- Easy setup and operation, perfect for beginners.
- Capability to use multiple tool types for varied applications.
Factors to Consider When Buying a CNC Machine for Aluminum Cutting
When considering an investment in a CNC machine for cutting aluminum, several factors play a crucial role:
1. Budget
Determine your budget before starting your search. CNC machines come in a wide price range, and it’s essential to balance between features and costs.
2. Production Volume
Consider how often you'll use the CNC machine. For high-volume production, investing in a robust and highly capable machine may be worthwhile, whereas smaller shops may prioritize versatility and cost-effectiveness.
3. Support and Maintenance
Choose a manufacturer that provides excellent support and maintenance services. Reliable customer service can be a lifeline, especially for businesses that depend on their CNC equipment.
4. Future Upgrades
Technology evolves rapidly. Therefore, consider purchasing a CNC machine that allows for future upgrades or enhancements to keep pace with industry advancements.
Maintenance Tips for CNC Machines Cutting Aluminum
To ensure optimal performance and longevity of your CNC machine, regular maintenance is key:
- Regular Lubrication: Keep moving parts well-lubricated to prevent wear and tear.
- Keep the Workspace Clean: A clean work environment reduces contamination and enhances machine performance.
- Inspect Tools and Part Quality: Regularly check tooling for wear and replace them when necessary to maintain quality cuts.
- Software Updates: Keep software up-to-date for bug fixes and improvements that can optimize performance.
Conclusion
Choosing the best CNC for cutting aluminum can greatly impact your business's manufacturing capabilities. By understanding the essential features, evaluating various models, and considering important factors before purchase, you can find a CNC machine that suits your specific needs. Investing in a high-quality CNC machine will not only streamline your operations but also ensure high-quality output that meets industry standards.
For further information, resources, and a range of options, visit roc-tech.com.